Extruding: 3D printed potatoes¶
Path | Target | Duration | Skills |
---|---|---|---|
Discovery, Curiosity | kids or adults | variable | Biofabrication, Digital Fabrication |
Introduction and context¶
One of the most emerging developments that is currently growing rapidly in the field of industrial design, fashion and art is the creation of biobased materials, biofabricated in laboratories from microorganisms, bacteria and biopolymers.
3D printing can be mesmerising and what can be better for kids than breaking up technology into simple and comprehensible steps that they can follow! This activity combines additive manufacturing and biomaterial paste extrusion, showing the process of making three-dimensional objects from a digital file using a simple recipe that everyone can practice with a syringe. It helps the participants understand the design possibilities and limitations of both material and process.
In this activity, participants will learn the basics of this technology in an agile, fun and active way.
The activity is designed for a moderate number of participants, for being a demo activity each participant will get the opportunity to observe the different stages of the preparation of the biomaterial paste and extrusion processes. The ideal number is 8 to 12 people.
The activity aims at introducing participants to 3D printing with potatoes.
Learning Outcomes
- Understand what a Biomaterial is.
- Understand the concept of extrusion.
- Understand how 3D printing additive manufacturing works.
- Familiarize yourself with the basics of 3D printing.
- Experience the limitations of this technology.
- Discover the mechanisms and components of a 3D printer.
- Learn to prepare an extrusion paste.
- Recognize the appropriate consistency of the paste.
- Understand additive manufacturing through layers of material.
Target audience and context of use
Creatives and professionals, such as producers, designers, architects, biologists, SMEs, and companies with interest in sustainability and alternative innovative biobased materials. Take a look at the Rotation station workshop if you wanna run a biomaterial demonstration.
Also, children from ages 8 - 14, their teachers and parents. Schools with curricular interest in STEAM areas of knowledge, understood as the integration of science, technology, engineering, with the arts, and mathematics. The target audience is also interested in promoting sustainability and alternative innovative biobased materials.
You can run the activity in different places like a university, a lab, a cultural center, a museum, etc. Set up a collaboration between your lab, and the selected institution.
Recommended number of attendees (8-12 or depending on Covid regulations) and facilitators(2 to 3). It would be great to invite someone to document and take pictures of your activity!
Preparation and materials¶
Dive into the references provided in this page, select your recipes and create your team of facilitators. Organize some testing sessions and brief meetings for coordinating with facilitators.
Be careful. Check you have all the tools and materials needed and that you will have time to wrap up your tools, set up the logistics for the event room.
Prepare in advance:
- Paste for extrusion
- Files for 3D printing (script, possible geometries, etc)
Equipment, Tools and Materials
- Table + Chairs
- Video recording and photo set up
- 1 scissors
- 1 set of plasticized sheets of paper or cardboard to print on
- Several 20 ml syringes
- Mixing bowls
- Measuring Jar
- Spatulas or big spoons
- Air Compression 3D paste extruder (ANYCUBIC KOSSEL PRO or similar)
- 125g Bag of instant Mashed potatoes (1 bag)
- 500-600ml Water
- 5-10g Of xanthan gum
- Kitchen paper
- Optional : Food coloring gels (different colors) Note: scale the amounts according to the total amount of paste to prepare for the attendants to the activity.
Step by Step Instructions¶
STEP BY STEP overview
- Fill the measuring jar with 500 - 600ml of tap water.
- Add the content of the package.
- Mix with the spatula until you get an homogenous mix. The mix should be thick rather than liquid.
- Touch the mix and try to form a shape with your fingers.
- Add the xanthan gum.
- Touch the mix again and feel how the gum gives elasticity and allows you to shape the paste with your fingers into little spheres or cubes.
- Take a syringe. Each participant can also try to replicate the same test in parallel.
- Fill in the syringe with some paste letting the air out.
- Push the bottom of the syringe, and see how the paste comes out in the form of a filament.
- Make a drawing with this filament on the plastified carton.
- Make the same drawing on top of the previous drawing, making several layers of material.
- In a 3D modelling software of choice (like rhino), model in mm a simple volume to print, taking into account the maximum size the printer (3D paste extruder) allows.
- The volume can be done through the extrusion of a closed or open curve. To begin, you can extrude a circle to get a cylinder, or a star.
- Take into account that through the extrusion of the paste, the printer will not provide any kind of support to the piece, so we need to consider the shape has stability.
- In a visual programming environment (like grasshopper) set the parameters for printing, including horizontal slicing distance, nozzle diameter (2-4mm), speed, etc.
- Once the figure is ready, copy (ctrl+c) the code from the visual programming environment.
- Load the tube with the paste, avoiding to leave bubbles or air inside the tube.
- Select the nozzle and place it firmly on the tube front end, close the tube’s rear.
- Place the tube on the printer and connect it to the air pressure system.
- Turn on the air pressure, set the desired pressure from 1.5 to 3 bar.
- Calibrate the 3D printer. NOTE : It is highly recommended that the facilitators go through this process several times before the activity, and ideally have previous experience, so they are knowledgeable of the correct parameters for the particular machine that is being used.
- Place a piece of paper or cardboard (ideally plasticized) on the base of the printer to then remove the printed piece.
- Go to the printer software (could be Repetier or similar).
- Paste (ctrl+v) the code taken from the visual programming environment.
- Set home, including in Z direction the height of the plastified cardboard base.
- Print.
Safety rules & Tips
- Use a lab coat or apron for keeping yourself clean
- Tie your hair up
- Use goggles when handling the air pressure system
Flyer for participants
Tips to facilitate the activity in context (to-do / not do)¶
For the better understanding of the materials, it is recommended to have samples to demonstrate the outcome of the recipes.
Always consider to find local providers.
References¶
-
More information about the Remix El Barrio exhibition and tutorials that participants can visit and look at. tutorials
Licence and credits¶
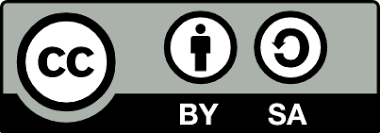
Attribution — ShareAlike CC BY-SA This activity has been designed, manufactured and coded by Santi Fuentemilla, Xavier Dominguez, Eduardo Chamorro, Lina Sofía and Manuela Reyes of the Future Learning Unit of the IAAC Fab Lab Barcelona and Powered by Cosmocaixa.It was adapted in the context of shemakes.eu for the biomaterial workshop with the Design Hub Museum of Barcelona.
Related and supporting activities/modules
It can be combined with the other topics of Biofabrication.